Current Projects
Atmospheric-Pressure Microplasma Jet Effect on Biomatter
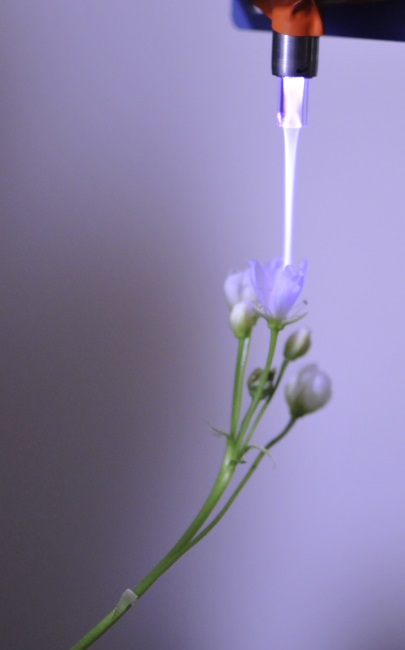
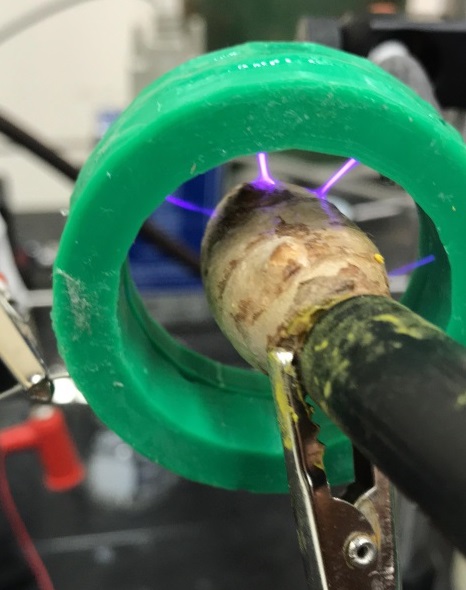
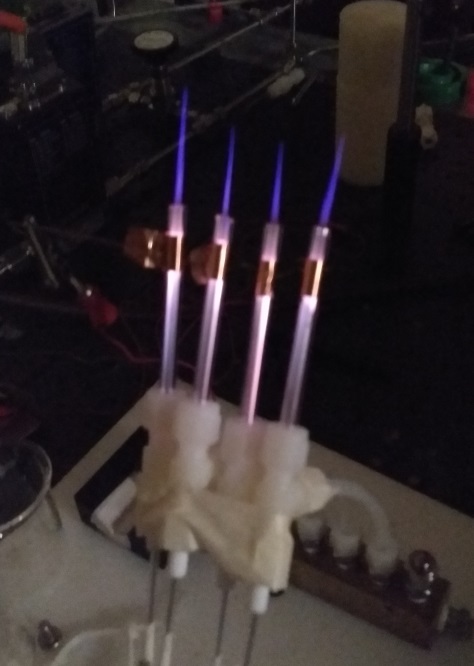
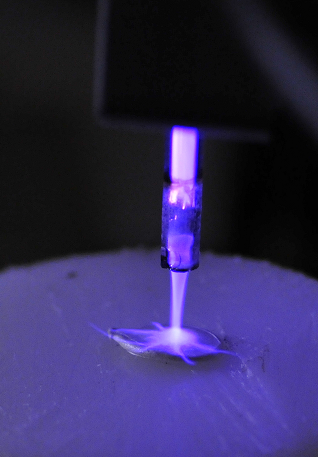
This project studies low temperature plasma treatment of plants, seeds, food, materials, and bacteria for beneficial applications such as decontamination, disease treatment, fungicide, and protective coatings. We partner with collaborators in chemistry, agricultural science, and food science. This work is funded by NSF, DHS, DOE, and industry.
Rotation Detonation Engines
This project studies the operation and performance of rotating detonation engines (RDE). A racetrack-style RDE has been tested with propane, methane, hydrogen, and oxygen propellants. The current work looks at injector behavior and wave dynamics. This work is funded by NASA and DoD.
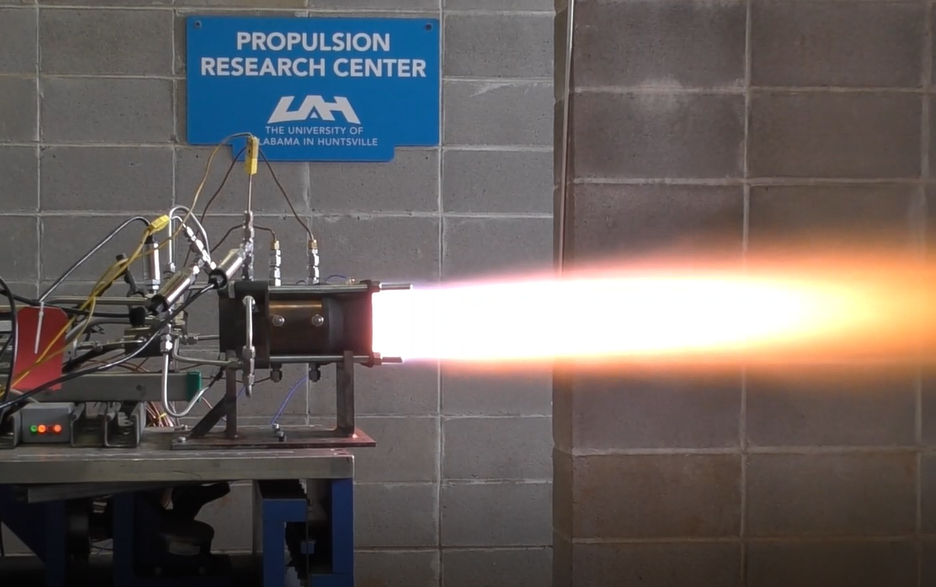
Plasma Interactions with Strong Magnetic Fields
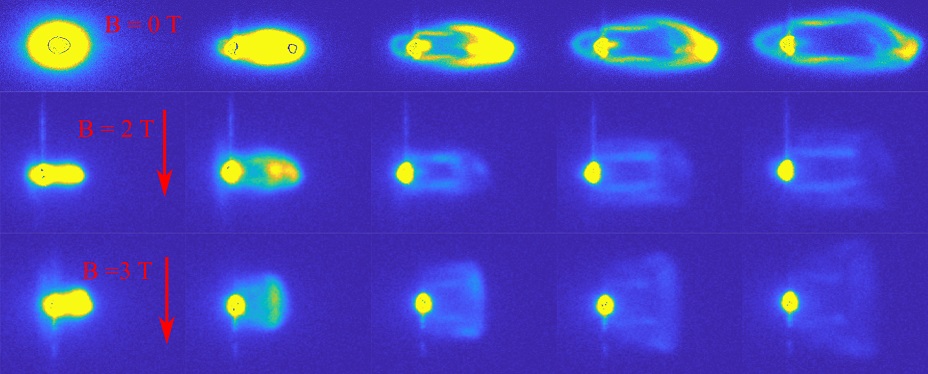
This area covers a couples of different project all focused on studying how strong magnetic fields interact with high-density plasmas. Applications include magnetic nozzles for pulsed fusion propulsion, astrophysical plasma shocks, and magneto-inertial fusion. The work in this area is sponsored by NASA, DOE, and NSF. A recently experiment was conducted to image plasma deflection in steady state magnetic fields. The image above shows a laser plasma expansion in a low pressure argon background with and without magnetic field. The experiment was done at Auburn's MDPX facility.
Torisional Magnetic Reconnection Propulsion
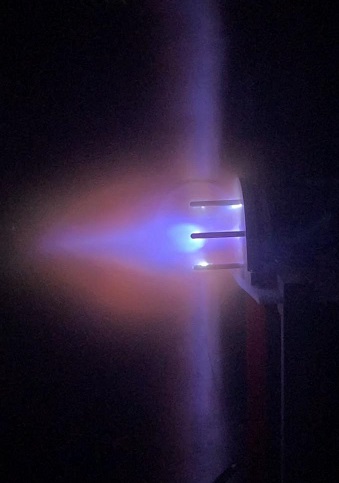
This project is studying the 3D magnetic reconnection phenomenon seen on the Sun. One application is for advanced space propulsion. The research is supported by the DOE and NASA.
Plasma-Liquid Interactions
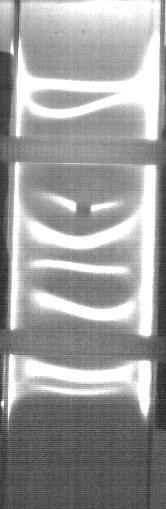
This project is part of the statewide NSF EPSCoR project and focus on plasmas generated in water mist for bio applications.
Variable Pressure Plasma
This project studies the effect of collisionality on plasma properties and behavior from low vacuum (~100 mTorr) up to atmospheric pressure. The project is supported by the NSF EPScoR project.
Past Projects
Atmospheric-Pressure Micro Plasma (AMP) for Nanomaterial Generation
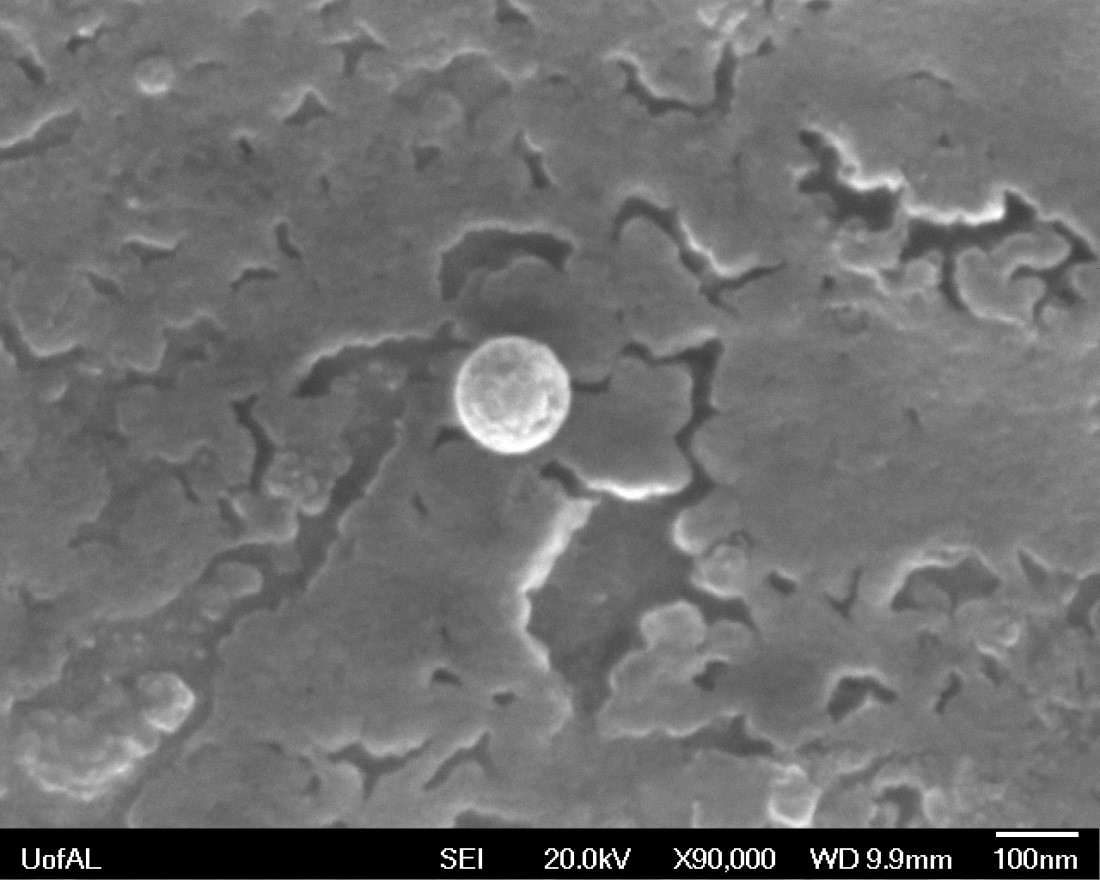
This project sought to understand the behavior of microplasmas at atmospheric pressures. Due to the greatly increased pressure and thus particle density compared to more conventional vacuum plasmas, some of the basic interactions changes. One example is the plasma is very collisional and gas temperatures can be close to room temperature. One aspect of this research is developing the diagnostic tools to measure the plasma properties which are required to understand the plasma behavior and interactions. Application-wise, we sought to use these microplasmas for the controlled and pre-determined synthesis of nanomaterials over large areas and understand the physics that control the material formation.
Electric Field Modified Combustion
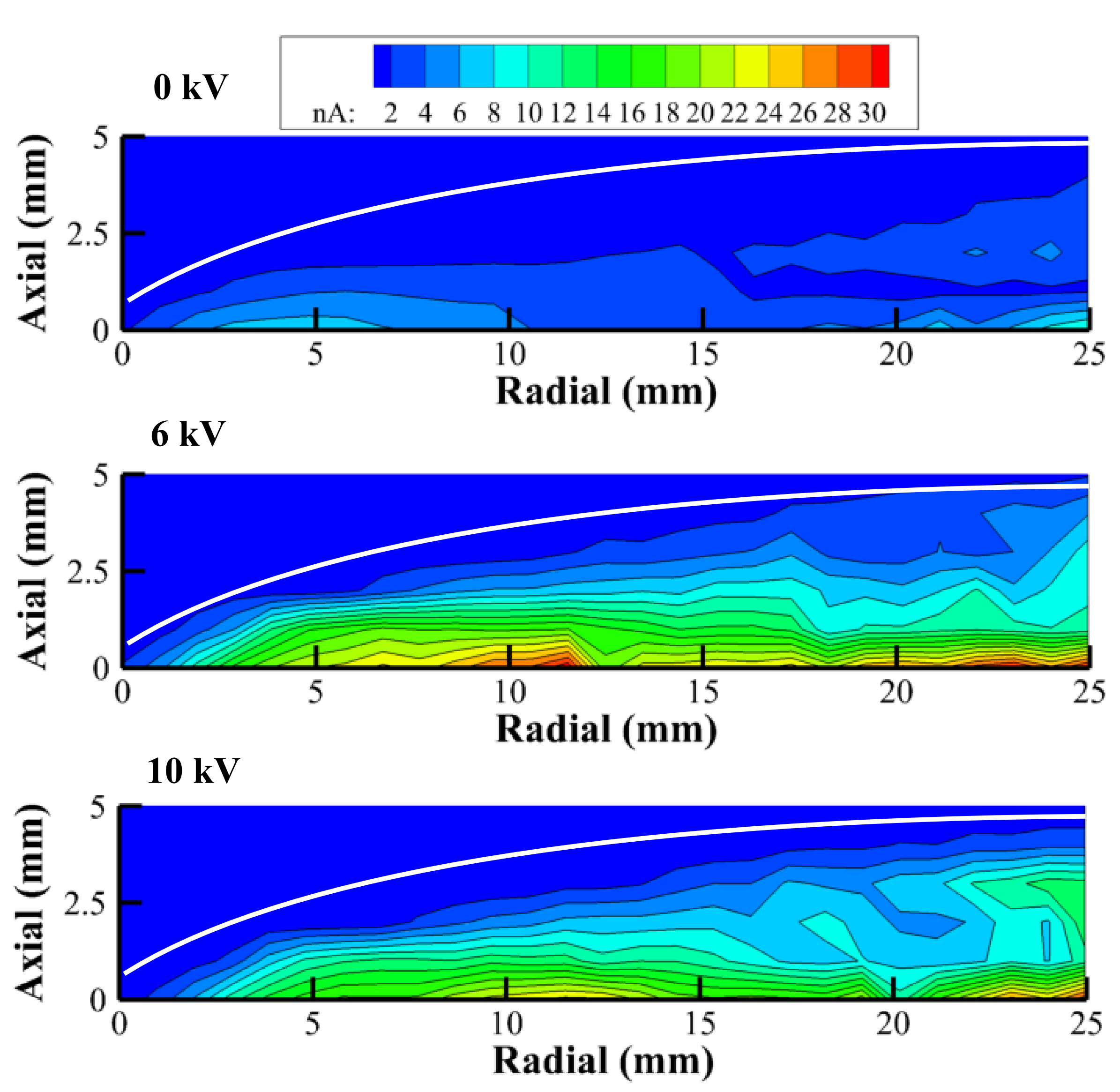
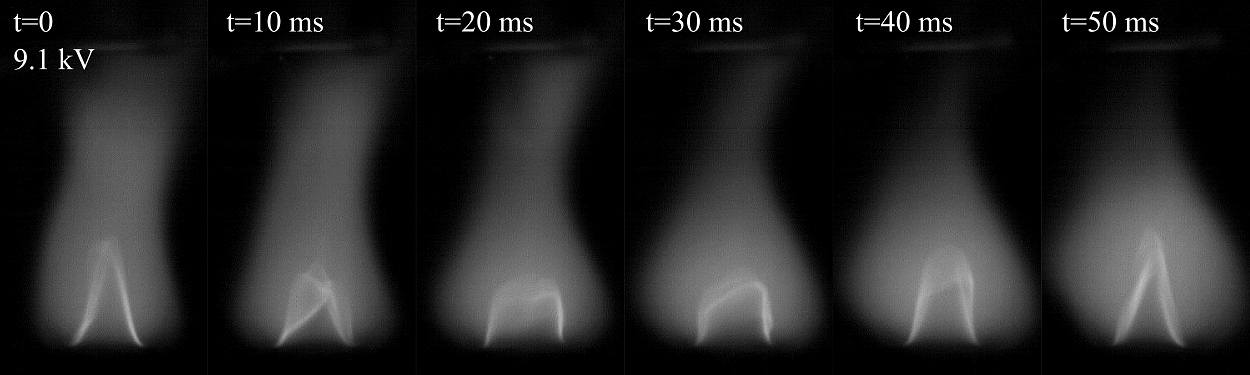
This work is part of the field called Plasma Assisted Combustion (PAC) where plasma and electromagnetic fields are used to modified by the combustion process and the flame behavior. Some of the effects include increase flame speed, increase flame height, reduced turbulence, and ultra lean combustion. This project evolved from DC fields on a flat flame burner to electric field effects with a pentad rocket injector in a closed combustion can. It is a blend of plasma, combustion, and propulsion.
Additive Manufactured Miniature Hall Thruster
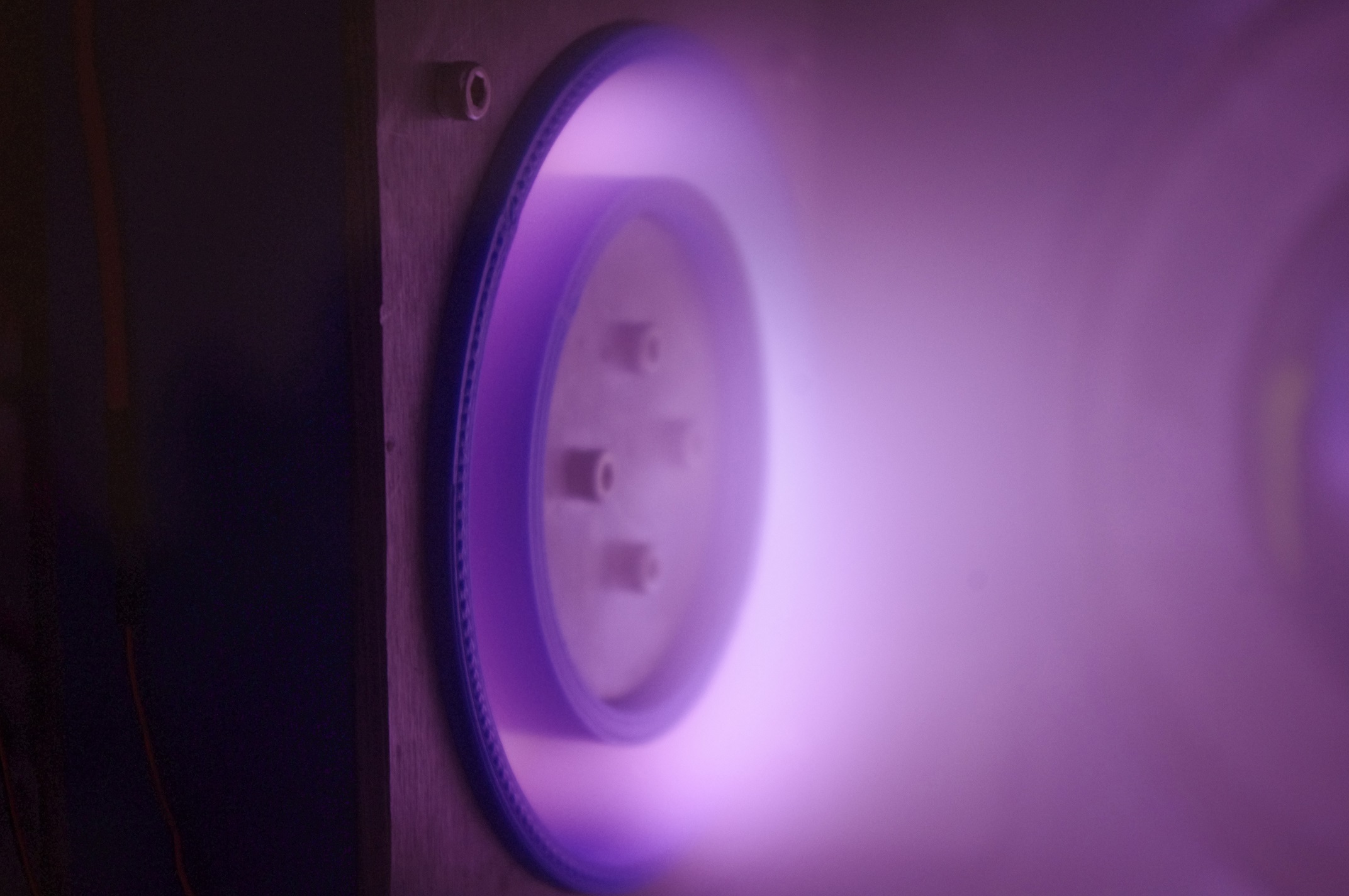
This project sought to design, built, and test a 3D printed miniature Hall thruster with a CubeSat foot print. The use of 3D printing allows more complex structures to be built, allow propellant and cooling channels to be printed directly into the thruster, and can reduce material and mass with lattice structures. Our initial prototype was build from ABS plastic using a commercial desktop 3D printer at the lab. In total there are 10 major parts of the thruster as the main body, discharge channel, and propellant distributor are build as a single piece, greatly simplifying fabrication and assembly.
High-Pressure Microplasma Regimes and Properties
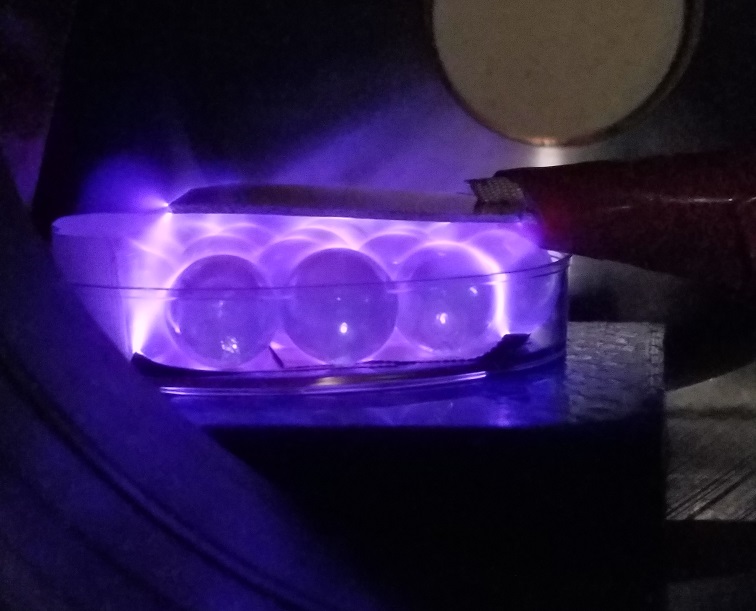
This project was in collaboration with the SMAP Center and funded by the Army SMDC. The project sought to understand the regime transition and the properties of arc, streamer, glow, and corona in a near atmospheric pressure rare gas discharge. An atmospheric pressure He-Ar plasma can serve as the gain medium for lasers, similar to Ar-ion or HeNe lasers. These new rare gas lasers could provide very high power levels. However, at high pressure, glow plasmas are confined to millimeter or smaller scales, which make it difficult to use as a gain medium. Thus we studied both the plasma and method to increase the plasma volume.
Pulsed Breakeven Fusion for Advanced Propulsion
This was a collaboration with Dr. Jason Cassibry to study regimes of pulsed plasmas for possible breakeven fusion for application to future in-space fusion propulsion. We did optical and spectroscopic diagnostics of the plasma generated by the high current pulsed discharge.
Time-Resolved Measurements of Plasma Striations
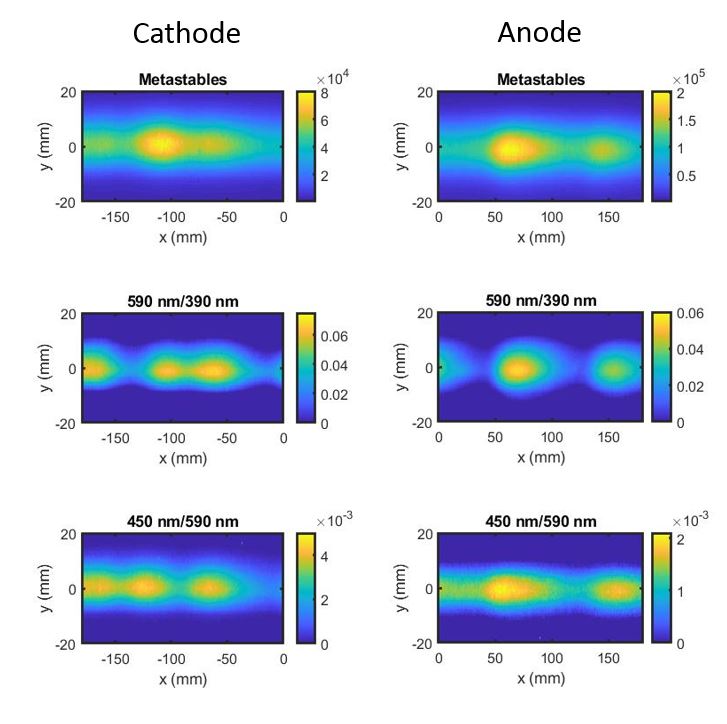
This project studied the formation and behavior of plasma striations in low pressure plasmas. Striations are localized packets of ions and electrons which can move or stand still. We used probe and optical diagnostics to study the formation and propagation of these striations in a dc discharge. This work was part of the NSF EPSCoR program.
Plasma Self-Organization
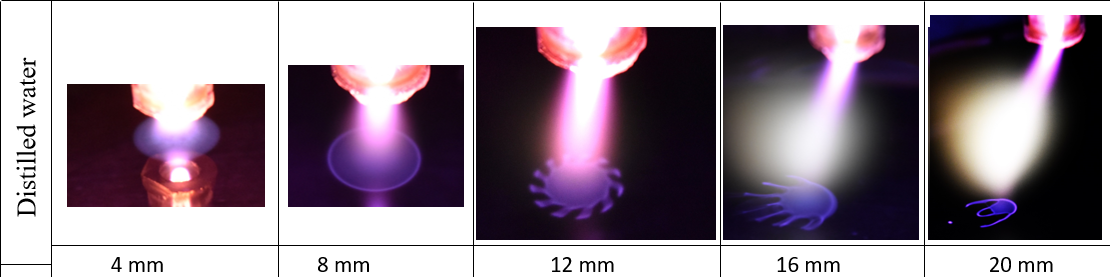
This project studied the ways plasmas can form coherent structures and patterns naturally. This was a collaboration with Dr. Vladimir Kolobov in CSPAR and a small business, CFDRC. We did experiments on plasma spots, plasma-solid interfaces, and plasma-liquid interfaces. The images above show the formation of self-organized patterns from a helium atmospheric pressure plasma jet on a distilled water anode. The project was funded by DOE.
Split-Ring Resonator Plasma for Space Micro Propulsion
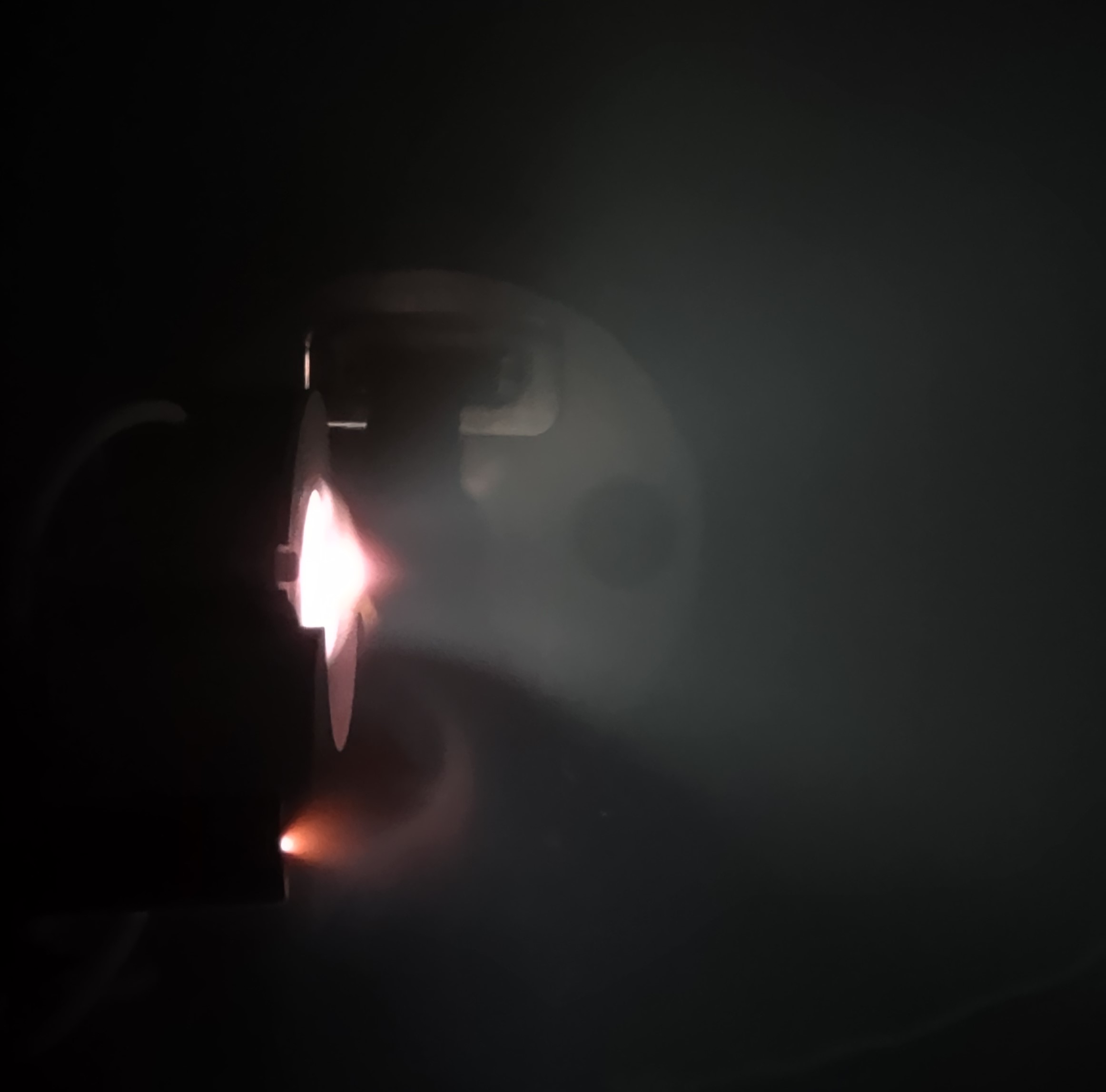
This project developed a new micro propulsion system for spacecrafts, especially small satellites like Cubesats. The thruster used a split-ring resonator to generate a microplasma, a method not yet seen in propulsion. The research studied how the resonator parameters affects the generated microplasma and how that can improve the thrust and specific impulse of a thruster. The plasma source was tested in a miniature ion engine and a miniature Hall effect thruster.